B&Wの製造はハンドメイドの工程がとても多い、むろんロボットも入れていますがB&Wのスピーカーのような製品は機械化しづらいため手加工は必須(というより不可避)です。
ハンドメイドを有難がる人が多いですが、正直言わせていただくと品質面では一般的にあまりいいことはないです。
ただ管理が特別ならば別。B&Wのそれはスペシャル、しかも学校みたいに厳格。
いい工場です。
(広告)
Amazon
本・ムック
Kindle楽天Books・Kobo
ワーシング工場がやっていること・組み立てと塗装
主力工場はサセックス州ワーシングにあります。作るのは800D4シリーズとオリジナルノーチラスのみ。
製造工程はざっといえば4種類
- 外注先が作った部品を受入検査する
- 組み立てる
- 塗装する
- 検査して出荷
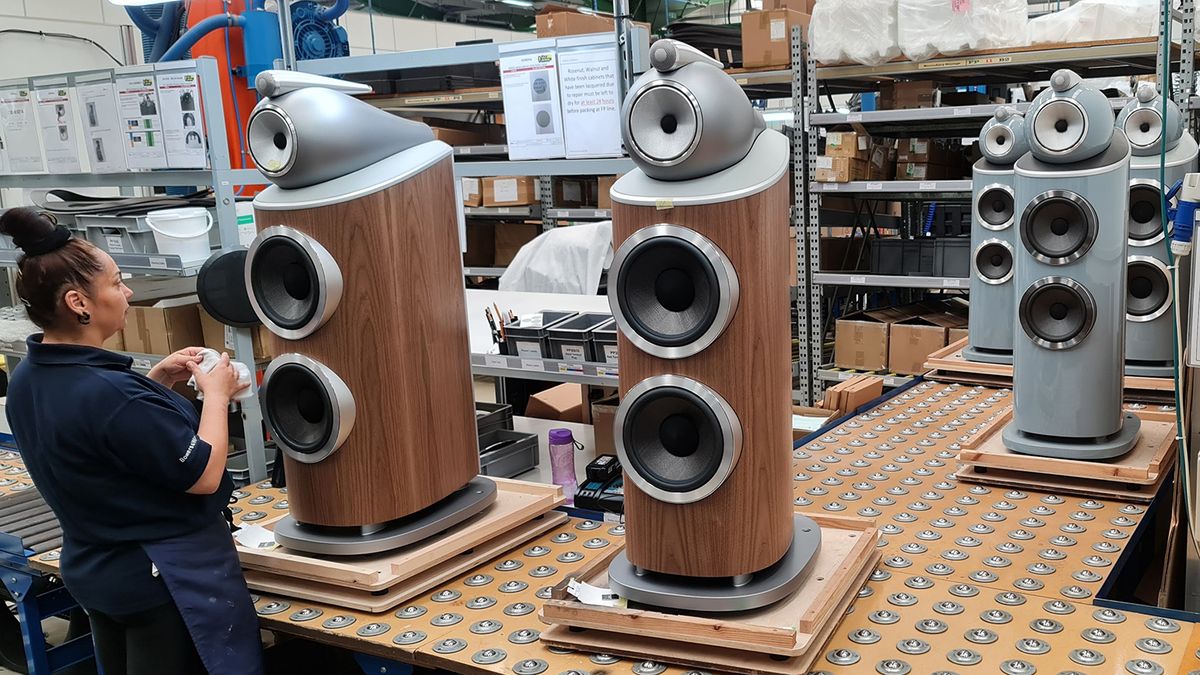
Via “Inside the Bowers & Wilkins factory to see the new 800 D4 speakers”(What Wi-Fi official website https://www.whathifi.com/features/inside-the-bowers-and-wilkins-factory-to-see-the-new-800-d4-speakers)
生産能力はキャビネット製作工程が常に上限となる
生産能力は非公表、ただし樺材合板を曲げるキャビネットプレスは5台分。これが能力の上限です。
あの樺材の合板を曲げて作るキャビネットは一番手のかかる工程のようです。歴史的に見てもBowers and Wilkinsが内製と外注を繰り返して試行錯誤してきた部門です。
キャビネットの製造公差は±0.2mm
木工については個人的に部品として扱ったことがないのですが、プレスなどの金属部品の組み立て公差が±0.1mmというのは珍しくありませんから、あれだけの大きさでしかも木製のキャビネットが0.2mmはかなりの水準ではないかと思います。
なお単純に手配から納入までの時間が長い部品という点で考えれば
ムンドルフが手配している電子部品(先行手配を含めれば3ヶ月)
または
「中国で製作している重要な部品」(手配+輸送期間が長い)
が一番納期が掛かると思いますが、それは原材料からの手当に時間がかかるからです。実際の部品製作の時間は短い。
その点で部品そのものを作る時間が長いという点では、組み立てから塗装まで含めた工数が多いキャビネット制作に最も納期がかかると思われます。
キャビネットづくりは長年かけて改善され続けた・24時間操業だった時期がある
なお現在は不明ですが、ある時期(2013年前後)B&Wのキャビネット製作部門は24時間の連続操業だった時期があるそうです。
夜間に作られたキャビネットに当たるのはあんまりぞっとしませんが、とにかくB&Wの製造に関する情報を集めるとキャビネット工程はとても時間の掛かる工程で、いろいろな工夫を試した上で今に至っていることがわかります。

Via “ARTIKELBOWERS & WILKINS PRODUCTIEPROCES”(hifi.nl official website https://hifi.nl/artikel_pagina2/7372/Bowers-&-Wilkins-Factory-Tour-Productieproces.html)
800D3で公称リードタイムは6〜8週間とされていました、現状はどうなんでしょう。
定番のトヨタ生産方式(TPS)も2003年にはやったそうです、印象的なのはR&D部門も参加していたそうで、現場管理だけでなく製品設計から合理化しようと取り組んだらしい。
今もそうかはわかりませんが(多分やっていないと思います)、以下の現場作業の様子から相当の管理水準にあるのは確かです。これは中国生産を始める上で他社にはないすごい強みになったと思います。
(広告・Amazon)Fire TV Stick 4K - Alexa対応音声認識リモコン付属 | ストリーミングメディアプレーヤー
超高精度・必ず二台1組(左/右)同時に作る(修正も)
英国工場の生産ラインは製作から検査まで全部2台1組で流動させるとのこと。
これはすごい。
B&Wはハンドメイドかマシンかという議論とは別次元だと思うのはここです。何をするのも2台同時というところを徹底させている。
ファンの贔屓だろと思われては困るので、プレス機が5台というのはなぜ?と思ったことは正直に申し上げます(木工プレス機は壊れたときの修理が大変なのでなんとなくわかりますが)。
とにかくどんな加工・検査も左右ペア同時に行うそうです(シリアルNoは1台毎です、念の為)。
これは品質、そして音のため。ペアになるスピーカーは最終の測定だけでなくそもそも製造条件までも極力同一にする。
単に管理規格を厳しくしただけの左右ペアリングではありません。測定には現れない、例えば使う塗料の量や製作する作業者の個性までできる限り同じにする。
音質面のすごいポイントです。
コストは掛かります。もし片方に不良がある場合ペアの片方が良品でも両方同じ再加工をするそうです。不良発生の割合については(当然ながら)What Hi-Fiの取材でも明らかにされていません。 再加工の工数はかなり掛かっていると思います。
すごいのはその現場の作業手法です。
英国工場のハンドリングは素手・「品質」は作業者の爪すら管理
B&Wの工程では作業者は以下の指示を守るのが必須です。
- 作業者の爪の長さをチェック
- 製品のハンドリングは素手(極力グローブをしない)
- 会社指定の作業着を着用(服のボタンやジッパー・ベルトのバックルで製品を傷つけない仕様のもの)
- アクセサリー・腕時計は禁止
少なくとも2013年時点ですでに現場管理の基本だったそうです。
スピーカーは素手でハンドリング
落とさない・傷をつけない、というだけではありません。
厳重な傷防止の対策を施した上で、製品を触った感触を知ることが高品質を実現すると知っているらしい。
すごく印象的です。製造現場はグローブごしでは感じ取れない品質情報がたくさんあります。
製品とこういう接し方をしている作業者は、色とか手触りとかで不良品がわかるようになる。
自分の仕事でも経験がありますが、こういう工場では測定器でも検知できない不具合を色や手触り、振動などで見抜く「魔術的なスキル」の作業者が本当に現れます。
間違いなくこの工場には「良品か不良か迷ったらこの人に見てもらえ」というウルトラスキルの持ち主がいるはず。
この場合の「ウルトラ」クラスとは例えば塗装面の出来(つまり数μm単位の差)を光の反射や色合いで見分ける感覚を持つ人のこと(少なくとも日本にはいます)。
またこれは入社したての素人から超ベテランまで、作業スキルに応じた管理体制をB&Wが確立しているということも意味する。
中国生産品でも図抜けて高品質なはずです。
海外転職サイトではB&Wの評判は良くない(指示が細かいから)
なお英国の転職情報サイトも日本のように「会社の評判」クチコミを載せていますが、B&Wは給与は悪くないとかすごくやりがいがある仕事という人がいる一方で
「マネージャーがやかましい」
「マネージャーの面倒臭い指示に応えないと給料が上がらない」
「細かい指摘をするマネージャーばかりで嫌」
という書き込みがとにかく多い。
爪の話をするんではさぞかし嫌われるだろうな〜と。言う方も大変でしょう。
なお爪の長さについてすこし申し上げますと、製品管理では重要なことですが海外ではやってもらうのが大変なことです。
露骨に膨れっ面をされたりとストレートに抵抗されます。
身だしなみや意識というだけでなく品質管理に直接影響するのですが、日本国内の工場ですら最近は説明してもなかなか理解してもらえない人が出てきています。
海外記事でも爪の管理に関してライターはジョーク混じりにとらえていました。海外では一般的にそういう感覚だと思います。
本当はかなり本質の会話です、恐れ入った。
Bowers and Wilkinsは高度の「品質管理手法」を持っている会社です。
かつて「嫌なら買うな」だった英国人がここまで意識を変えてくるとは。本当に頑固なくせに良いとわかった時の思い切りがいいのは連中のすごいところ。
塗装はロボット8割、人2割(キャビネット限定)
800D3シリーズの実績でいえば圧倒的にブラックが人気だったそうです。この塗装は12回。
大きく分けてサンディング(下地作り)と塗装の2種類の作業ですが、これも2台同時でしかも片方に問題が見つかると両方やり直し。
なおキャビネット塗装は8割ぐらいの作業はマシンが使えるそうですが、タービンヘッドのような曲面のみの構成ではやはりロボが使えないそうです。
サンディングから塗装まで全部人手でやる。
この調子でダイヤモンドツィーターやコンティニュアムコーンの製作から全体の組み立てまで全てやっているそうです。
(広告・Amazon)SONY デジタルカメラ Cyber-shot RX1R 2470万画素 光学2倍 DSC-RX1R
部品受け入れは厳しい・ネジは10個につき1個の検品
繰り返しますが、B&Wは外注先での製作比率が高い。自社工場は組み付けと塗装・検査だけといってもよろしい。
このスタイルは製造業では一般的ですが、その代わり外注部品の品質管理を厳格に、しかも効率よくやらなきゃならない。
外注管理にしくじると簡単に採算割れします。
前回も申し上げましたが、B&Wは例えば使うネジは10個につき1個の精度確認だそうです。
大きなものや高価なもの、つまりムンドルフのネットワークとかデビアスのダイヤモンド振動板(500ポンド)は全品ということはご想像いただけるかと。
一方でネジぐらいならば10個に1個ならさほどの負担ではないと思われるかもしれません。
同じ管理をしている会社を実際に見たことがありますが、物凄いストレスです。
これをやっている会社の現場では作業者は見学されることも嫌がる、気が散るからです。こちらもこわごわ少し離れてみる。
こういう管理で作る製品は最低10年ノントラブルを目的とした高耐久の産業機器で行われるものです。
本・ムック暗い低音は好きじゃない! ~ダブルウーファーズ会長のオーディオ探求~ (CDジャーナルムック)
B&W・この「管理能力」ならば中国生産もやれる
いや、ここまで知りますとね、そりゃ問題のないものは中国部品も使わないとコスト面では無理だろうと思いますよ。また彼らならば中国ベンダーを使いこなせるでしょう。
オール英国なんてしたら1,000万ぐらい平気で行く、と思ったら気づきました。
オリジナルノーチラスがいつの間にか1,000万円になっていた(1993年当時500万円/ペア)。
800シリーズは将来値上がりする、というかもう少し上のクラスで勝負するようになるだろうと思っていますが、ここの製造現場はもうその準備が完了しています。
ハイエンドではなく完全にトップエンドを作る場所です。
改めて製造について、B&Wは3つのすごい財産を持っています。
- 手作業の現場スキルの上/中/下の基準と指導・管理方法
- 外注先の管理方法
- 膨大な不良例のデータ
何をすれば上手くいき、何をすれば不良が出てくるのか。全部経験してモノにしている。
つまりこの会社が中国で作るなら、多分上手くやるはずと申し上げたい。
実際中国ではいきなり大きく展開しませんでした。英国人らしく少しづつ、着実に。英国とは作業内容内容も変える。
次回申し上げますが自社工場を立ち上げるまでかなりの長期間Rotelの工場を使い続けていました、用心深いです。